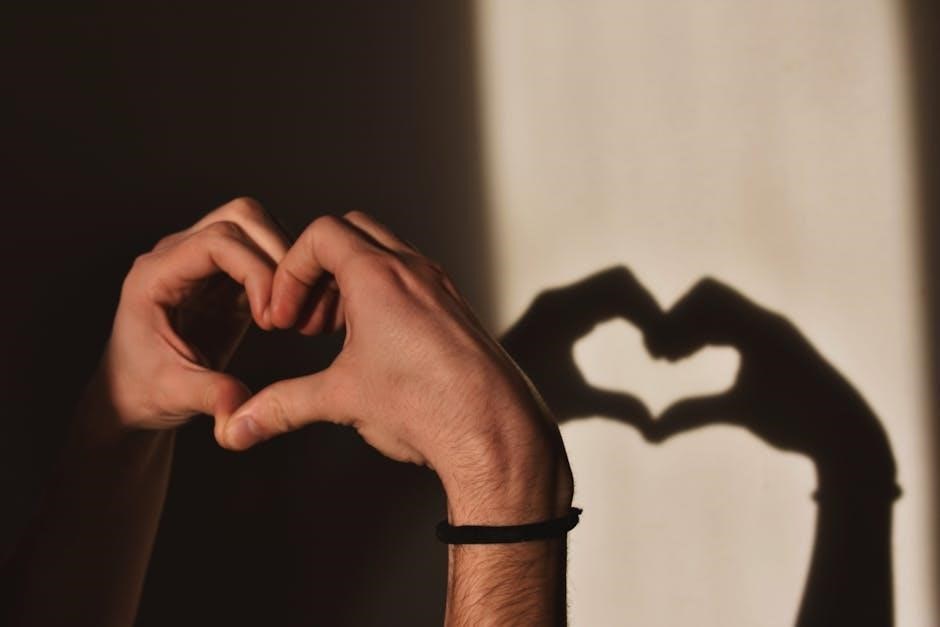
Understanding CNC Manuals
CNC manuals are critical for operating and maintaining CNC machines․ They provide essential information for setup, troubleshooting, and understanding machine capabilities․ Referencing the manuals ensures safe and efficient operation, prolonging the machine’s lifespan․
Various CNC manuals exist, including operation and maintenance instructions for CNC lathes, systems, and inverters․ Configuration manuals detail customer-specific CNC system requirements․ Understanding the different types is crucial for effective machine management and optimal performance․
Importance of CNC Manuals
CNC manuals are indispensable resources for anyone working with CNC machines․ They serve as comprehensive guides, offering vital information for a range of tasks, from initial setup and operation to troubleshooting and maintenance․ Proper utilization of these manuals is paramount for ensuring the safe, efficient, and effective use of CNC equipment․
These manuals detail machine specifications, operating procedures, and safety protocols, reducing the risk of errors and accidents․ By consulting the manual, operators can optimize machine performance, minimizing downtime and maximizing productivity․ Furthermore, CNC manuals often contain detailed diagrams and troubleshooting guides, enabling users to diagnose and resolve issues independently․
They provide a deeper understanding of the machine’s capabilities and limitations, fostering informed decision-making and preventing costly mistakes․ Investing time in understanding the CNC manual is an investment in the long-term health and productivity of the machine and the operator’s expertise․
Types of CNC Manuals
Navigating the world of CNC machining requires familiarity with different types of manuals, each serving a specific purpose․ Operation and maintenance manuals are essential for understanding day-to-day operation and routine upkeep of CNC lathes, systems, and other components like inverters․ These manuals detail procedures for starting, operating, and safely shutting down the machine․
Furthermore, they outline preventative maintenance schedules and troubleshooting steps․ Configuration manuals provide instructions for setting up CNC systems according to customer-specific requirements․ These might include network settings, parameter adjustments, and software configurations․ Programming manuals detail the G-code language used to control the machine’s movements and functions․
Finally, component manuals provide in-depth information on individual parts of the system, such as drives, motors, and control panels․ Understanding the different types of CNC manuals and their respective content is crucial for effectively managing and utilizing CNC equipment․
Connecting a CNC Machine Manually
Connecting CNC machines manually often involves Ethernet connections․ This allows for network integration and data transfer․ Different connection methods exist, requiring specific configurations outlined in the CNC manuals․
Ethernet Connection Methods for CNC Machines
Connecting a CNC machine to an Ethernet network offers numerous advantages, including remote monitoring, program transfer, and centralized data management․ Several methods facilitate this connection, each with its own requirements and configurations․ One common approach involves directly connecting the CNC machine to a local network using a standard Ethernet cable․ This requires configuring the machine’s network settings, such as IP address, subnet mask, and gateway, to match the network’s parameters․
Another method utilizes a network switch or router to connect multiple CNC machines and other devices to the same network․ This allows for seamless communication and data sharing between machines and a central server․ Furthermore, some CNC machines support wireless Ethernet connections, providing greater flexibility in placement and eliminating the need for physical cables․ However, wireless connections may be less stable and require careful configuration to ensure reliable data transfer․
Consulting the CNC machine’s manual is crucial for determining the supported Ethernet connection methods and the specific configuration steps required․
Configuring Network Settings
Configuring network settings is essential for establishing communication between a CNC machine and other devices on an Ethernet network․ This process typically involves assigning a unique IP address to the CNC machine, along with a subnet mask and gateway address․ The IP address identifies the machine on the network, while the subnet mask defines the network’s address range․ The gateway address specifies the router or device that allows the machine to communicate with external networks․
The specific steps for configuring these settings vary depending on the CNC machine’s control system․ However, most systems provide a network configuration menu or interface where these parameters can be entered․ It’s crucial to ensure that the IP address is unique within the network and that the subnet mask and gateway address match the network’s configuration․ Incorrect settings can prevent the machine from communicating with other devices, hindering data transfer and remote monitoring capabilities․
Refer to the CNC machine’s manual for detailed instructions on accessing the network configuration menu and entering the appropriate settings․
CNC System and Component Manuals
Comprehensive manuals cover CNC lathes and systems, detailing operation, maintenance, and troubleshooting․ They are vital for understanding machine functionality and ensuring optimal performance․ Refer to them for specific configurations․
Inverter manuals provide critical information about the inverter’s role in controlling motor speed and power․ These manuals detail setup, parameters, and troubleshooting, essential for maintaining efficient and reliable CNC operations․
CNC Lathe and CNC System Manuals
Comprehensive manuals for CNC lathes and systems are indispensable for operators and maintenance personnel․ These manuals provide detailed instructions on operation, programming, and troubleshooting, ensuring optimal machine performance․ They often include parameters specific to the CNC system, such as those required for Fanuc controls found in machines like the ACC 16F3 series․
These manuals detail the connections and configurations necessary for integrating components such as power cables (e․g․, 24 V DC for i-Series CNC / Power Mate) and digital drive systems․ Understanding these manuals is crucial for effectively using advanced features like closed-loop control and DRIVE-CLiQ connectivity․ They also guide users in interpreting technical specifications and utilizing optional configurations to meet specific manufacturing needs․ Furthermore, these manuals often include safety guidelines and procedures to prevent accidents and ensure safe operation․
Inverter Manuals
Inverter manuals are essential for understanding the operation, configuration, and maintenance of inverters used in CNC machines․ These manuals provide detailed specifications, wiring diagrams, and troubleshooting procedures, ensuring optimal performance and longevity of the inverter․ They describe how to connect the inverter to the CNC system and motor, outlining the proper voltage, current, and grounding requirements․
Furthermore, inverter manuals explain how to configure parameters such as acceleration, deceleration, and motor control modes to match the specific needs of the CNC application․ They also include safety precautions and guidelines for handling high voltages and currents․ Understanding the inverter manual is crucial for preventing damage to the inverter, motor, and CNC system, as well as ensuring safe and reliable operation․ These documents often cover fault codes and diagnostics, aiding in quick identification and resolution of issues․
CNC Machine Specifications
The 3020T triaxial engraving machine specifications detail dimensions, materials, and motor information․ Operating instructions outline proper usage․ These specifications are crucial for understanding the machine’s capabilities and limitations for specific tasks․
Standard motion control includes four axes (Z, X, Y, C) and supports rotary axis (C) control․ These specifications define the range and precision of movement, impacting the types of projects the CNC can handle․
3020T Triaxial Engraving Machine Specifications
The 3020T triaxial engraving machine specifications encompass vital details regarding the machine’s physical attributes, materials employed in its construction, and the characteristics of its motors․ A comprehensive understanding of these specifications is paramount for operators to fully grasp the machine’s capabilities and limitations․ The specifications also contain detailed operating instructions that guide users in the proper and safe utilization of the equipment, ensuring optimal performance and longevity․ These guidelines are essential for achieving precise and accurate engraving results․
Furthermore, the specifications document outlines the machine’s dimensions, workspace, and the types of materials it can effectively process․ It also details the power requirements, operating voltage, and any specific environmental conditions necessary for optimal operation․ By adhering to these specifications, users can minimize the risk of damage to the machine and ensure consistent, high-quality output in their engraving projects․ This comprehensive information enables informed decision-making and efficient utilization of the 3020T triaxial engraving machine․
Standard Motion Control
Standard motion control in CNC systems typically involves управлениядвижением по четырем осям (Z, X, Y, С), providing a foundational framework for diverse machining operations․ This control system often supports управление осью вращения(С), enabling more complex and intricate part creation․ The motion control system is crucial for coordinating the movements of the machine’s various axes, ensuring accurate and precise toolpaths․
Effective utilization of standard motion control requires a thorough understanding of its parameters and settings․ This includes configuring axis limits, defining feed rates, and implementing safety protocols․ Standard motion control is integral to achieving efficient and repeatable machining processes․ Furthermore, it allows for the integration of advanced features such as tool compensation and adaptive feed control․ Ultimately, mastering standard motion control is essential for maximizing the capabilities of CNC machinery․ By understanding the intricacies of standard motion control, operators can optimize machining processes․
HAL Configuration
HAL configuration involves defining pins and signals, crucial for connecting hardware components․ Each signal originates from a single source (HAL Dir out pin) and connects to multiple readers (HAL Dir in pin)․
Directional Signals (Dir In/Out)
HAL Pins and Signals
HAL (Hardware Abstraction Layer) configuration necessitates a thorough understanding of pins and signals․ These elements serve as the fundamental building blocks for establishing communication between software and hardware components within a CNC system․ Each signal is characterized by a singular source, typically a HAL Dir out pin, which transmits data․ Concurrently, a signal can have multiple readers, represented by HAL Dir in pins, allowing for versatile data distribution across various modules․
The meticulous configuration of HAL pins and signals is paramount for ensuring the seamless and reliable operation of the CNC machine․ Incorrect or improperly configured pins can lead to malfunctions, communication errors, and ultimately, compromised performance․ Therefore, it is imperative to consult relevant documentation and adhere to established best practices when configuring HAL pins and signals to achieve optimal system functionality․ This configuration defines the flow of information within the CNC system․
Directional Signals (Dir In/Out)
Directional signals, designated as Dir In and Dir Out, play a pivotal role in managing the flow of information within a CNC system’s Hardware Abstraction Layer (HAL); A Dir Out pin serves as the source, transmitting a signal to one or more Dir In pins․ This configuration enables a single data source to be shared among multiple recipients, facilitating efficient communication between different components of the CNC machine․
The proper assignment and configuration of Dir In and Dir Out signals are crucial for the reliable operation of the CNC system․ Incorrectly configured directional signals can lead to data corruption, communication failures, and ultimately, compromised machine performance․ Therefore, careful attention must be paid to the directionality of signals when configuring the HAL to ensure seamless and accurate data transmission throughout the system․
CNC Keyboard and Drive Systems
A full CNC keyboard enables comprehensive machine control․ Paired with digital drive systems and DRIVE-CLiQ, it facilitates easy motor connections․ This setup allows for precise command execution and monitoring of CNC operations․
Closed-loop control systems, crucial for CNC machines, ensure accuracy through feedback; These systems continuously monitor and adjust motor performance based on real-time data, enhancing precision and minimizing errors during machining processes․
Full CNC Keyboard Functionality
A full CNC keyboard significantly enhances the operator’s control over the machine, providing a direct interface for inputting commands and parameters․ This comprehensive control extends to various functions, including axis movement, spindle speed adjustments, and program execution․ The keyboard’s design typically incorporates dedicated keys for commonly used functions, streamlining the operation process and reducing the need to navigate through complex menus․
Furthermore, a full CNC keyboard often includes features like emergency stop buttons and override controls, providing immediate access to critical safety functions․ The integration of a keyboard simplifies tasks such as tool offset adjustments and program editing directly at the machine․ Proper utilization of the full CNC keyboard is essential for maximizing machine efficiency and ensuring precise control over the machining process, contributing to higher-quality output and reduced downtime․ It also helps facilitate easier troubleshooting and diagnostic procedures․
Closed-Loop Control Systems
Closed-loop control systems are vital in CNC machines for ensuring accuracy and precision in motion control․ These systems utilize feedback mechanisms to continuously monitor the actual position and velocity of the machine axes, comparing them to the desired values specified by the CNC program․ Any discrepancies between the actual and desired values are immediately corrected by adjusting the motor drive signals, maintaining accurate positioning and minimizing errors․
The use of encoders or other feedback devices provides real-time data to the control system, enabling it to compensate for disturbances such as varying cutting forces, friction, and thermal expansion․ This continuous feedback loop ensures that the machine follows the programmed path with high precision, resulting in improved part quality and reduced scrap․ Closed-loop systems are particularly beneficial for complex machining operations and high-precision applications, providing reliable and consistent performance․